Paramone Industries
Information and profiles of the Chairman , Executive Chairman, Board of Directors, Senior Leadership, and Committee Members

AAC Blocks (Autoclaved Aerated Concrete)
Paramone Industries’ AAC blocks represent a groundbreaking innovation in construction materials, offering unparalleled strength, lightweight design, and eco-friendliness. Manufactured using fly ash, cement, lime, and aeration agents, our autoclaved aerated concrete (AAC) blocks adhere to IS 2185 Part-3 standards, ensuring exceptional quality.
As a superior alternative to clay bricks and concrete blocks, our AAC blocks embody the principles of green building, significantly reducing carbon footprint. Constructed from recycled materials with zero wastage, Paramone Industries’ AAC blocks accelerate construction by up to four times compared to clay bricks, thanks to their precise dimensions, ease of use, and reduced material requirements.
We offer a diverse range of AAC block sizes to cater to your specific walling needs, and our competitive pricing provides better value with faster construction and reduced material usage. With unmatched properties including being super lightweight, non-combustible, and offering exceptional thermal and acoustic insulation, Paramone Industries’ AAC blocks ensure a safe, durable, and comfortable living environment.
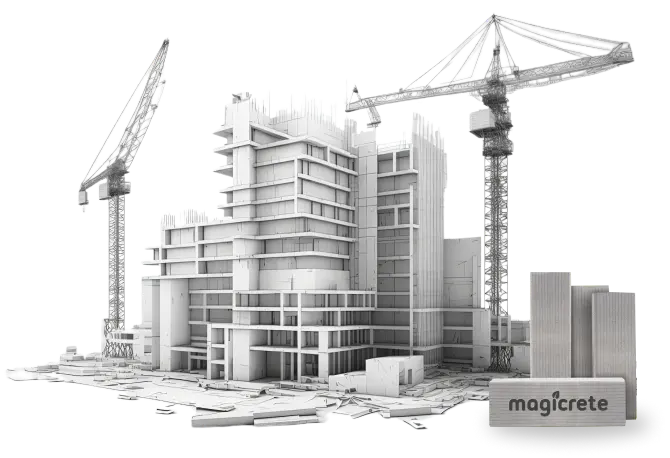
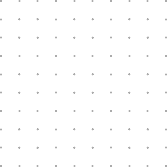
Years of service
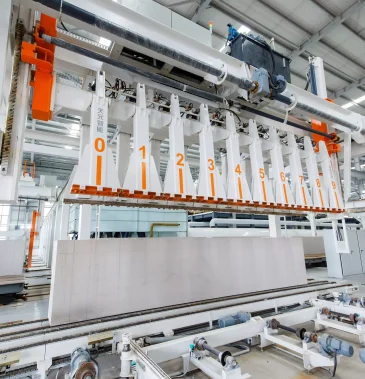
- Raw Material Processing: Our facility is equipped with a range of machinery, including jaw crushers, ball mills, and bucket elevators, to process and store raw materials with utmost efficiency.
- Automatic Steel Mesh Fabricating & Circulating: We employ cutting-edge technology to fabricate steel mesh (cage) required for panels, ensuring precise dimensions and flawless quality.
- Batching & Pre-Curing: Our expert technicians meticulously mix raw materials, pour them into moulds, and initiate the pre-curing process, laying the foundation for exceptional strength and durability.
- Cutting Section: With precision and finesse, our cutting machines demould, cut, and shape the green cake, transforming it into a robust and versatile building block.
- Autoclaving Section: Our state-of-the-art autoclave facility subjects the blocks to high-pressure steam curing, infusing them with unparalleled strength, density, and thermal insulation properties.
- Finished Products Packing Section: The final stage involves sorting, stacking, packaging, and transporting the finished AAC blocks to our storage yard, where they await dispatch to construction sites.
The Manufacturing Odyssey
Our AAC block manufacturing process is a symphony of precision, innovation, and quality control. The journey unfolds through six distinct stages
Unlocking the Benefits of AAC Blocks
Our AAC blocks offer a multitude of benefits that redefine the paradigm of building construction
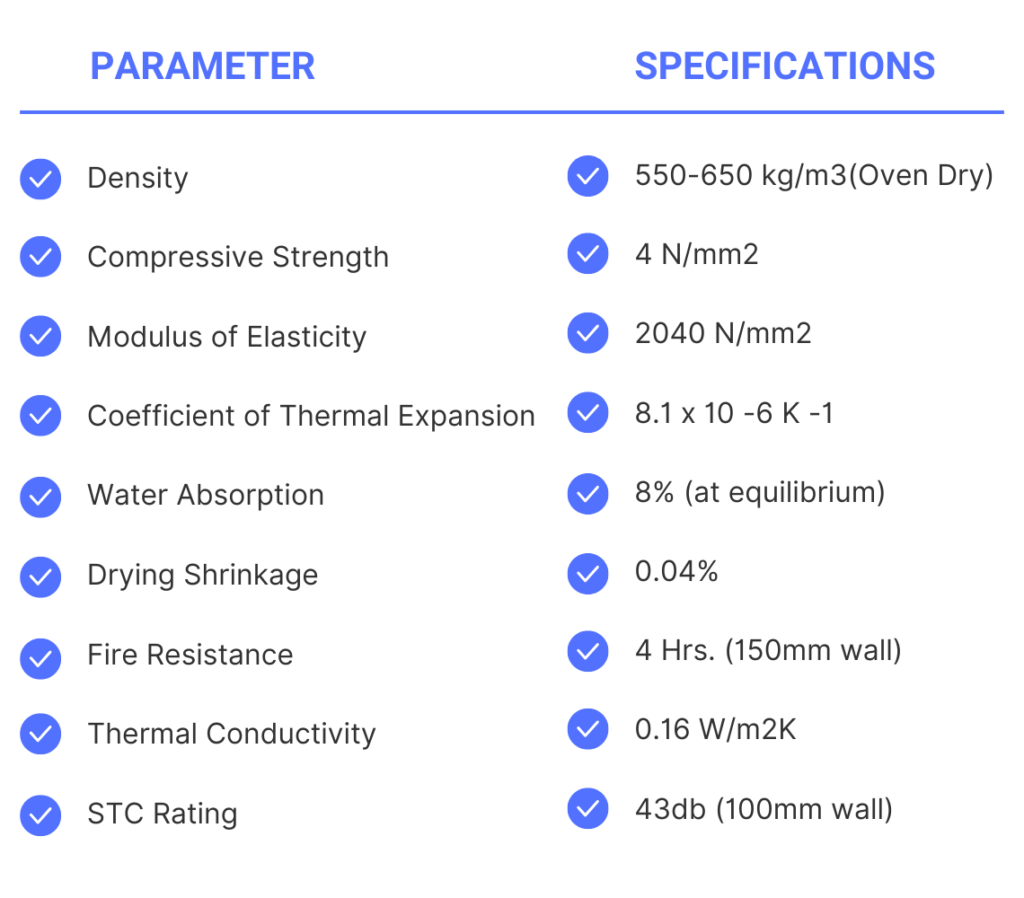
Walling Technology Comparison
Our AAC blocks are available in a range of sizes to cater to diverse construction needs. Size: 75mm, 100mm, 125mm, 150mm, 200mm, 225mm. Features: Lightweight, superior strength, thermal insulation, earthquake resistance, fire resistance, sound insulation
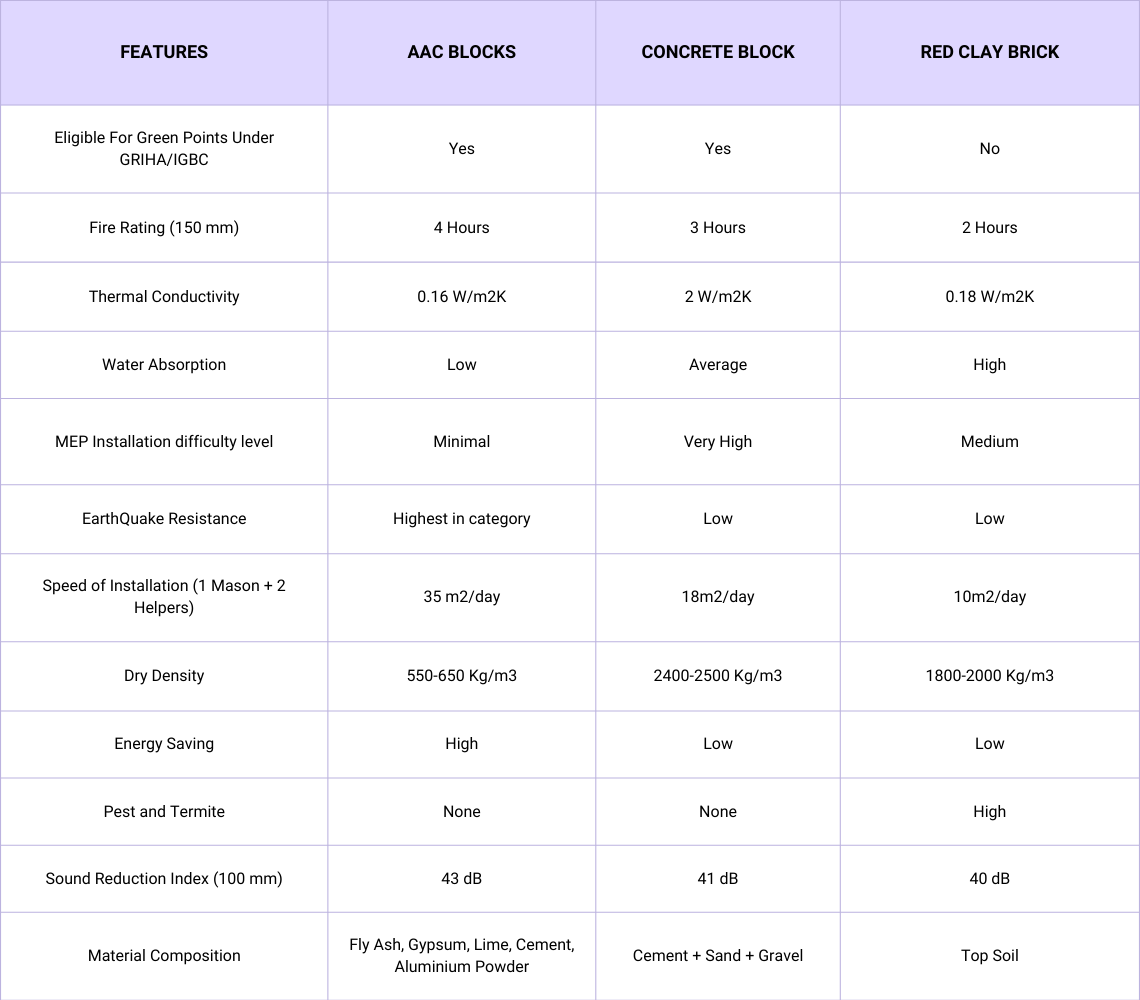
Walling Technology Comparison
Our AAC block manufacturing process is a symphony of precision, innovation, and quality control. The journey unfolds through six distinct stages
Get a Quote
If you’re interested in learning more about our AAC blocks or would like to request a quote, please don’t hesitate to contact us. Our team of experts will be delighted to assist you in choosing the perfect AAC blocks for your construction project.
Pawangroup1@yahoo.com
Phone
94253 11322
Address
Plot no. FA 38 Sceme no. 94 Near nakshatra hospital World cup square Indore